Gembox is a six-week project focused on developing a mould tool to create the form of a jewelry travel box.
Gembox combines functional craftsmanship with elegant design, offering a compact and stylish solution for keeping jewelry safe on the go.
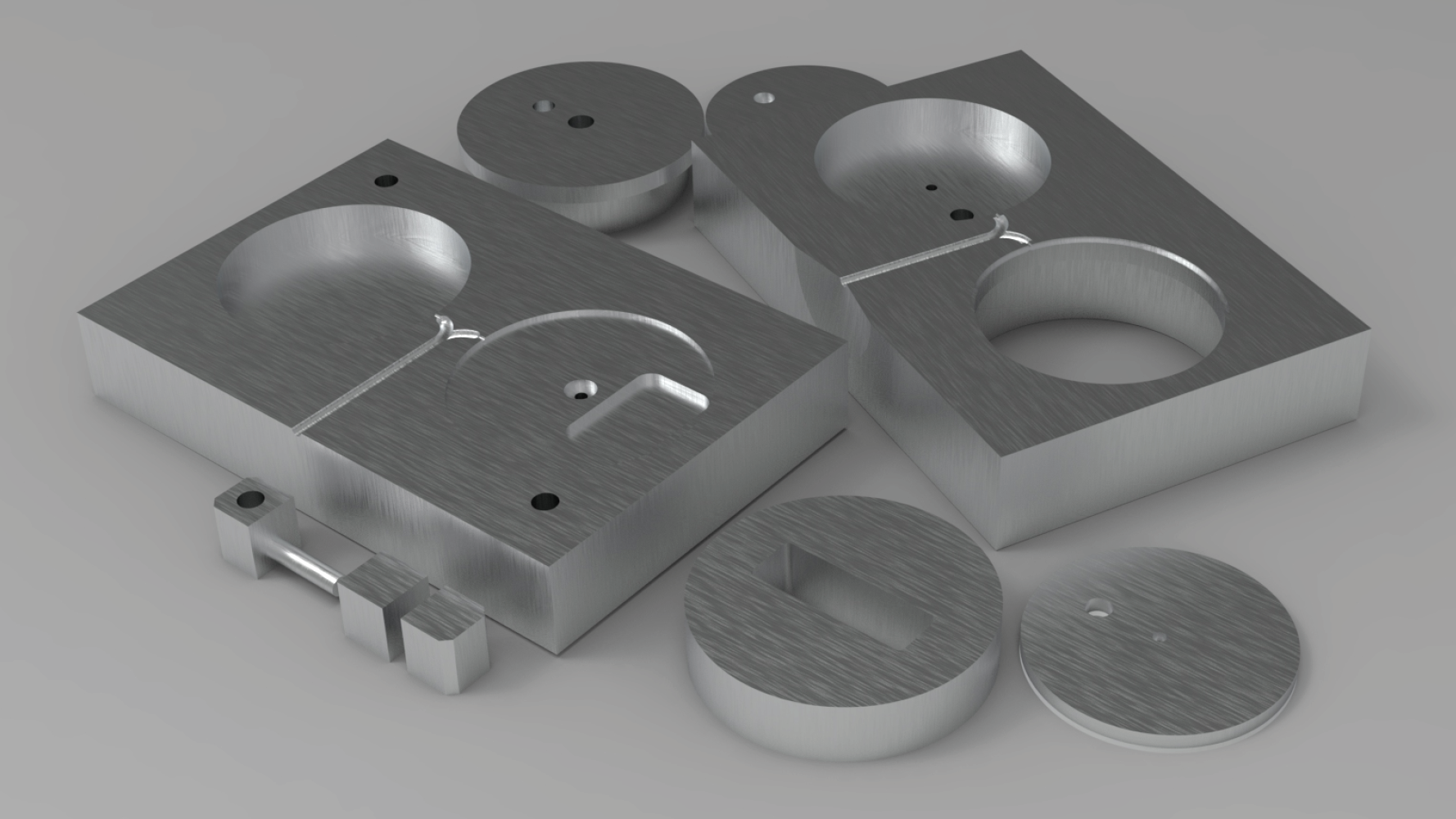
The Brief
Design and manufacture of an injection moulded promotional widget for a company or brand and the mould tool required to mould it.
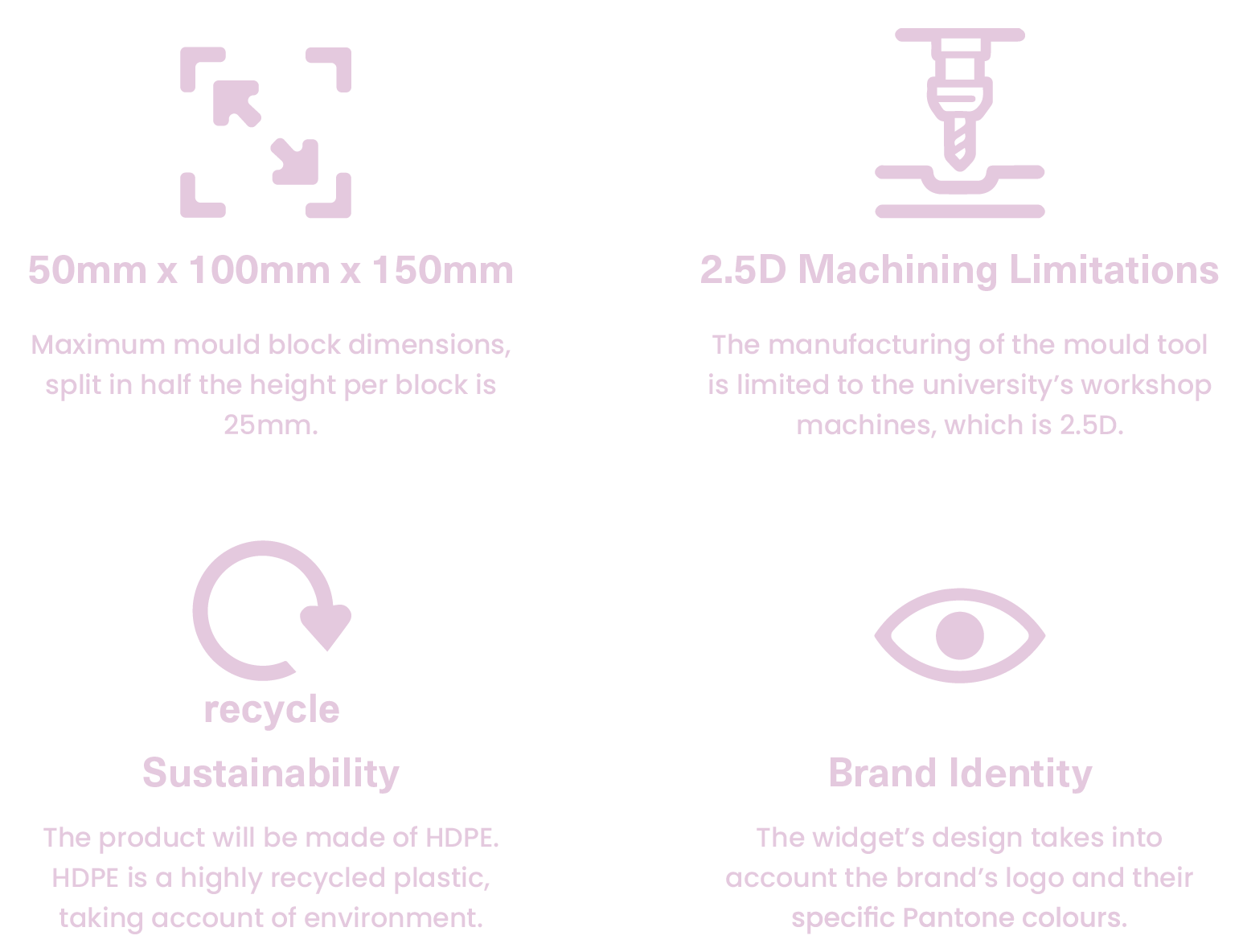
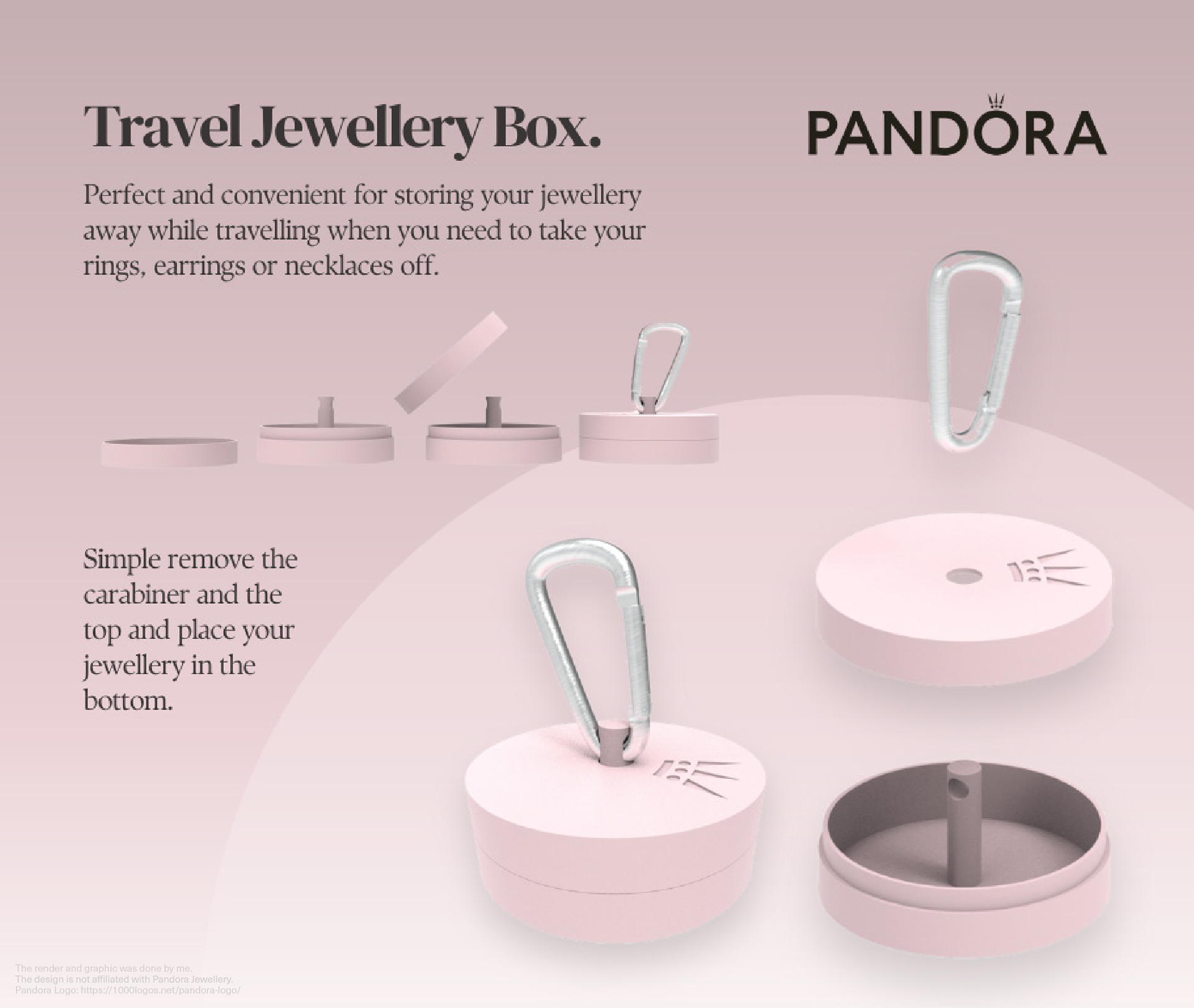
Poster Design
I created a promotional poster for Gembox to showcase my 2D and 3D skills, combining product renderings with cohesive branding. The poster highlights the craftsmanship behind the jewelry travel box and positions Gembox as a stylish, functional product.
The Mould Tool
Drawings of the mould tool layout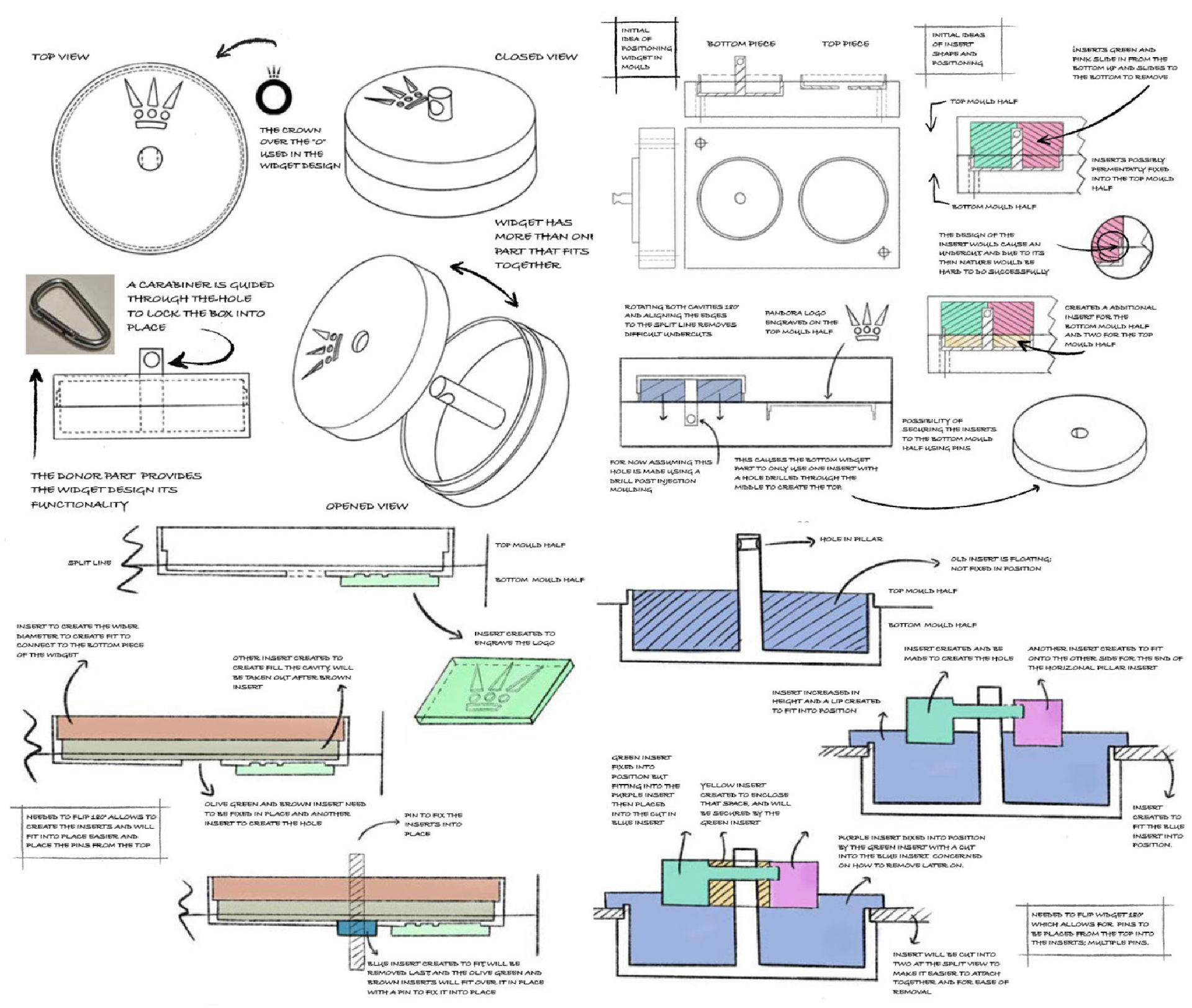
Manufacturing Considerations
The university’s machinery limits design complexity. The circular shape aids manufacturing, avoiding sharp corners. Fillets were added to non-circular shapes. Steel inserts were chamfered for easy removal. Precise positioning required, reflected in engineering drawings.
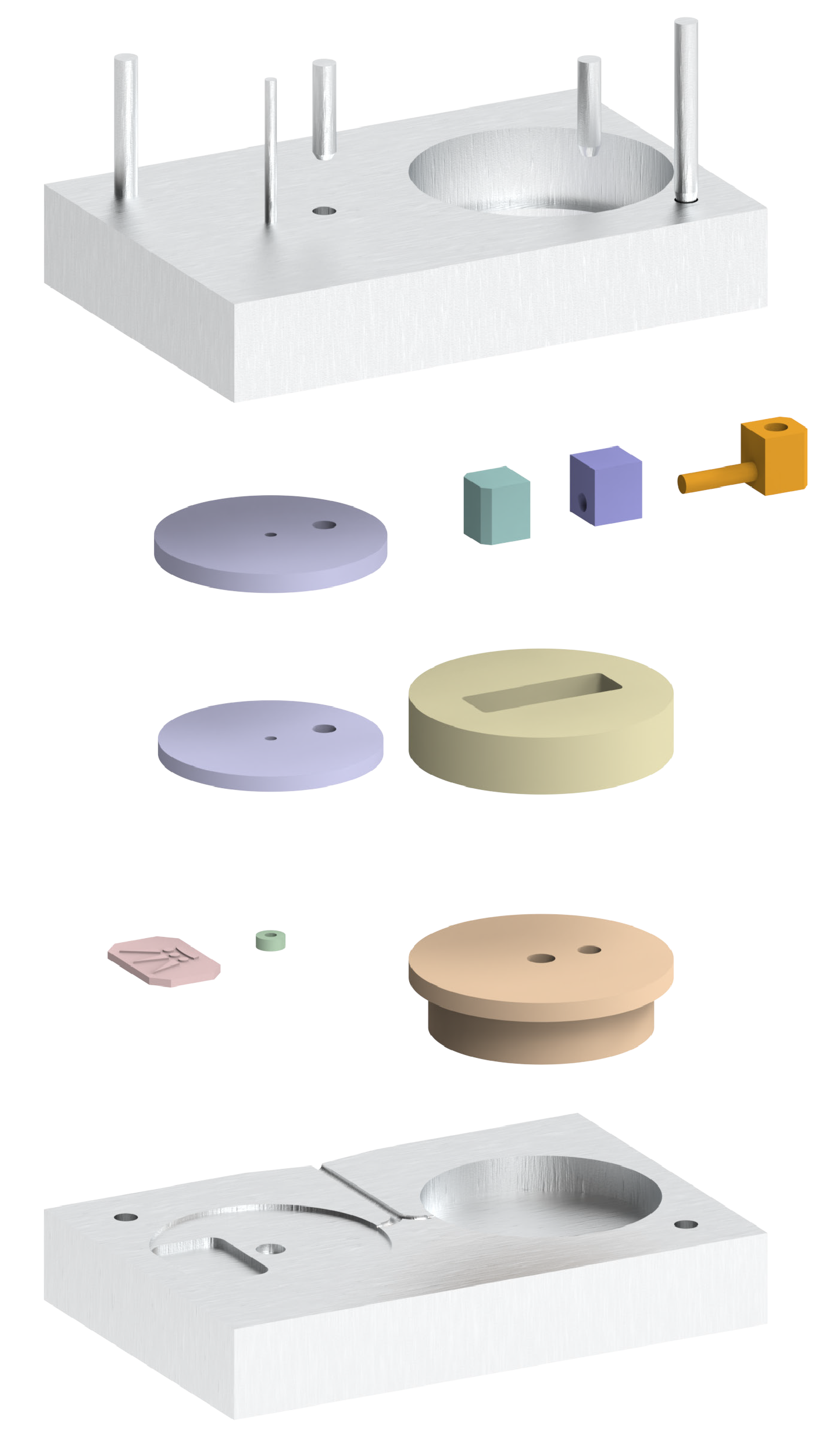
Plastic Simulations using SolidWorks
Solidworks Plastics flow simulations of the widget cavity: The overall mass of the plastic components is 14.00g and the mass of the carabiner is 4.00g, which is within the requirements of 28.00g of polymer.
The best material for the widget would be HDPE which has high stiffness and would help with the shown sink marks on the pillar of the widget. However, the plastic analysis was run in LDPE as that is the material available to use for the prototype.
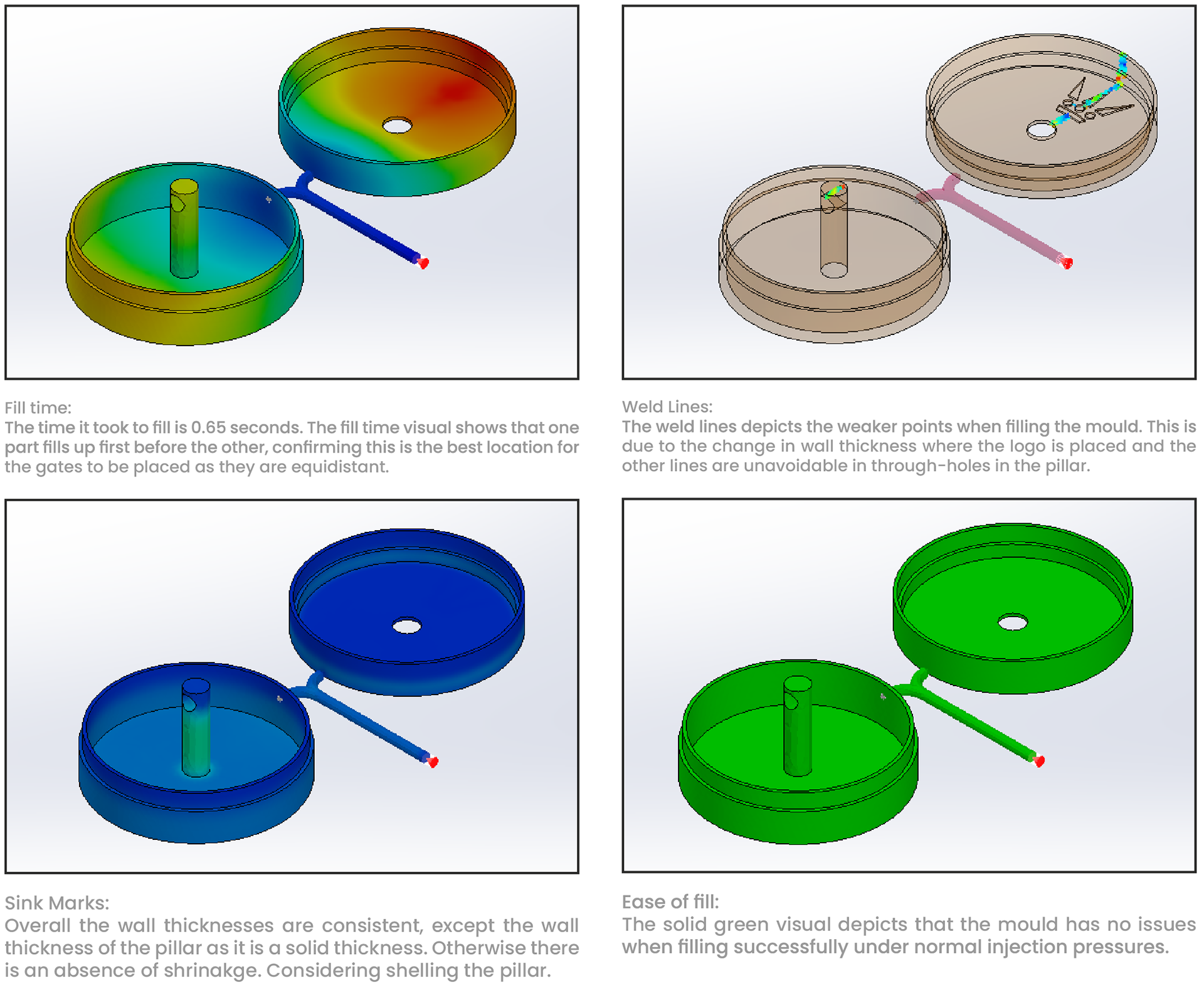
Engineering Drawings
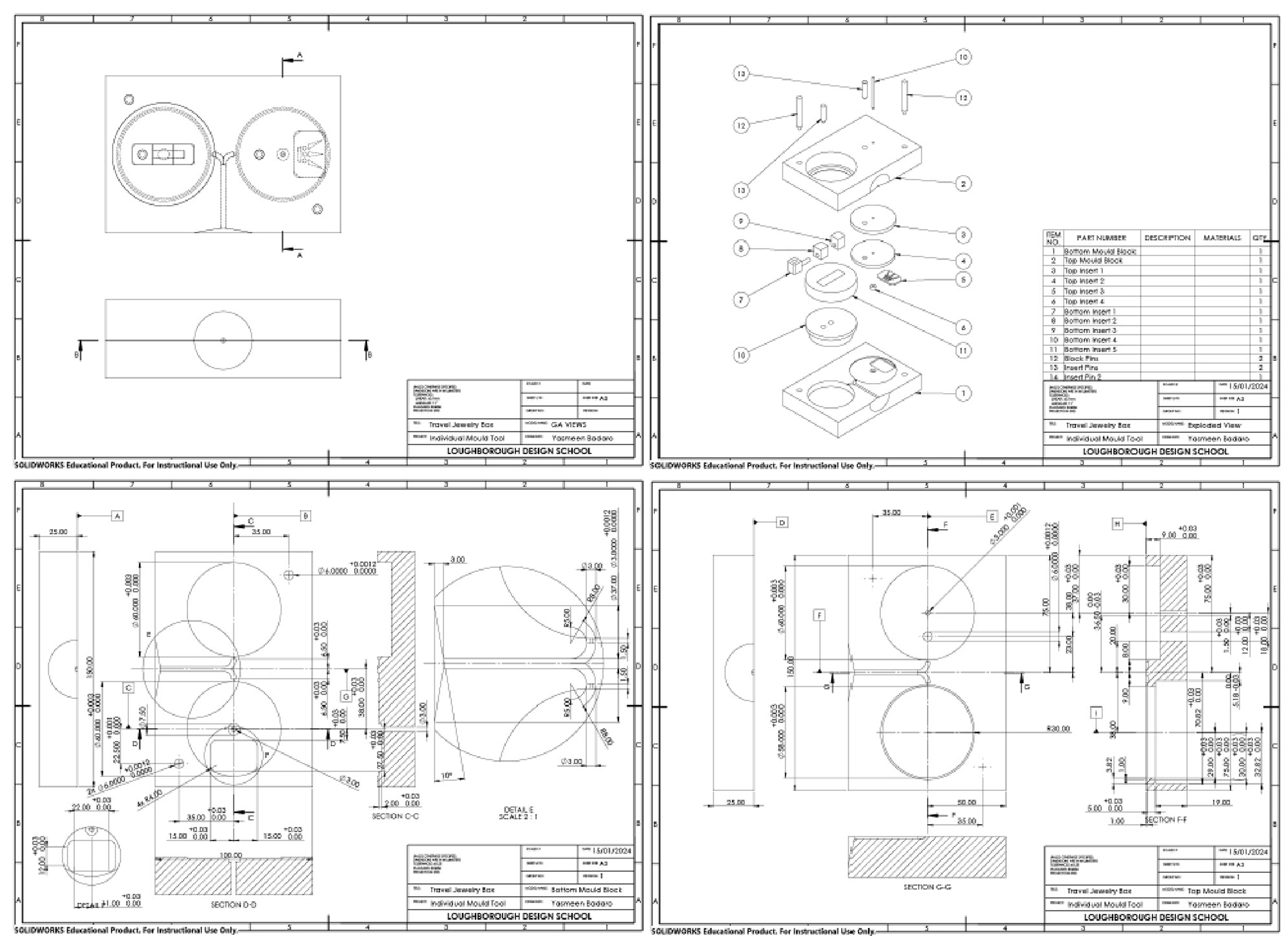
Toolpaths
Generation of CNC machining code: To understand the process when making the mould tool, CNC HSMworks toolpaths simulation was used on SolidWorks. HSMworks toolpath was simulated on the bottom mould tool. Surfacing the faces of the cavities and multiple passes with the drill will allow for smoother and accurate cuts when using CNC machining.
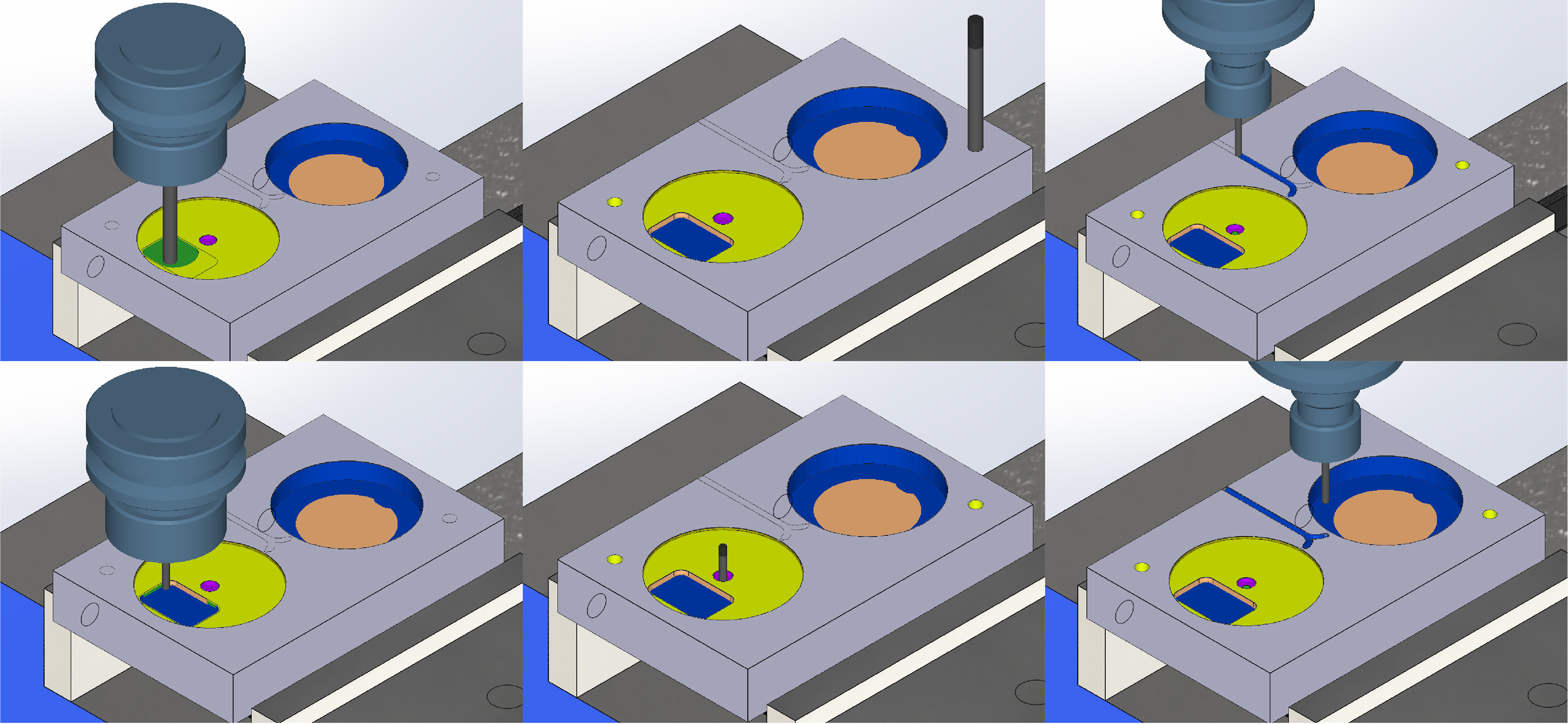